Behind the Brand | Nordica
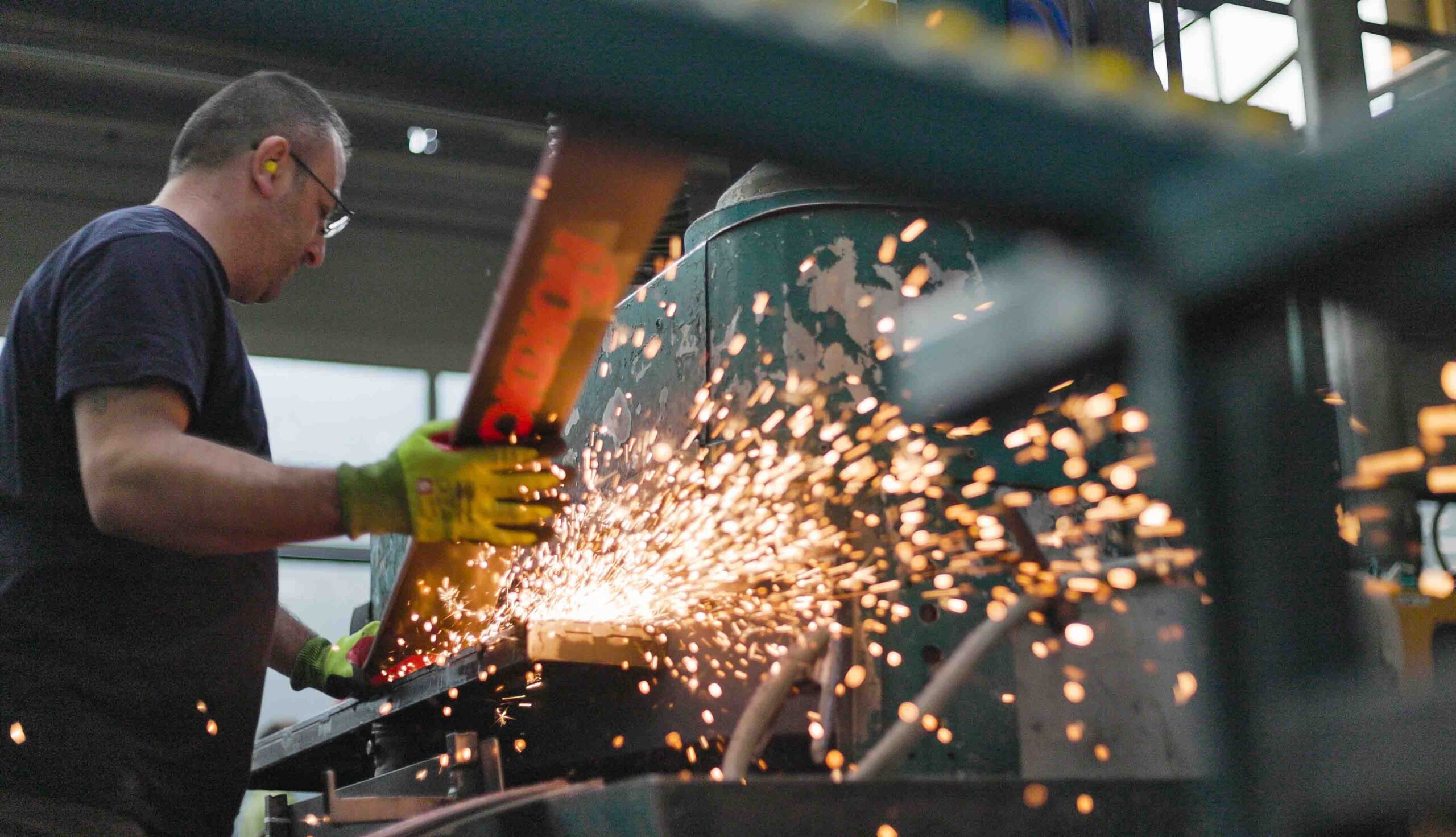
Al Morgan: Great to meet you, Manfred. Can you tell us a bit about yourself and how you ended up as the main ski guy at Nordica’s factory in Mittersill, Austria?
Manfred Reitsamer: Coming from outdoor sports and being a mountain guide for years, equipment has always been a key part of what I do. I’ve worked with various brands, giving me lots of experience in building and ideas about skis, especially construction techniques. With over 17 years in the factory now, I suppose I’m a veteran.
AM: Mittersill is a tiny mountain town, but it’s home to one of the world’s most renowned ski factories. How did this come about?
MR: This has been the home of Blizzard for over 75 years, a centre of innovation, developing ideas and products that make skiing better for all skiers. From introducing the world to polyethylene running bases to integrated metal and fibreglass to name a few. Now, as the home of both Nordica and Blizzard production, as the Tecnica group, we’re still pushing hard with new ideas to find that next level of enjoyment.
AM: We’ve heard other brands have sought the use of the facility on some projects. What makes building skis in this Austrian village so desirable?
MR: There’s a lot that makes Mittersill special. A ski made in our factory benefit directly from the local mountain economy, namely local staff, many of whom have been longtime employees. That level of local experience, and expertise in the people designing and building our skis, is really important.
Mittersill is perfect for ski R&D – we can have an idea, build a prototype and test it within an hour’s drive, nine months of the year. We can then make adjustments back at our desks, all within a short timeframe, with very little travel, so we can develop and test many ideas at once.
AM: Making skis in the mountains sounds like a dream gig! Talk us through a regular working day at Mittersill…
MR: [Laughs] The R&D office is full of passionate skiers. If conditions are good during winter, it’s not unusual for us to postpone work and go for a tour close by, to enjoy some powder turns in the sunrise. The office work is still part of the game though; a lot of stuff needs to be coordinated and adjusted with production. It’s incredibly satisfying going through the concept stages, making a prototype and it performing as you dreamed during on-snow testing.
AM: How many skis can you guys make in a day?
MR: At full capacity, we are able to press 1,000 pairs a day.
AM: Climate change is an important issue. What is Nordica’s approach to sustainability?
MR: We run the factory with green energy, mainly hydropower, and we installed solar panels on the roof five years ago. The Tecnica group first published its sustainability report in 2022. Our commitment to sustainability means we’ve already got a lot of initiatives in place, including recycled tip inlays, sidewalls, bases and steel edges for skis. Another piece that came out during our Life Cycle Assessment programme was the huge impact of carbon usage in the ski, so we’re working to move away from this material. These are just some examples of our commitment to the environment and sustainability.
AM: Backcountry touring has witnessed significant growth in popularity in recent years, partly due to Covid. In terms of the numbers of skis currently produced, how big is this ‘niche’?
MR: It’s true that Covid led to a boom in ski touring, but it was a slight anomaly. Thankfully, due the versatility of the new Unlimited boot and not having a pure uphill-orientated offering with our Unlimited skis, we’ve been able to manage a stable result. We’ll see the reality of the market after consolidation, but I would not be surprised if this number will still be over 10% of the total ski volume, especially in Europe.
AM: Ah yes, the Unlimited series; all-mountain touring skis based on the very successful Enforcer/Santa Ana skis. Given these are made for shredding the resort and earning your turns, how do these differ in construction?
MR: The main goal was to reduce weight, which we achieved by using lighter wood cores, lighter prepregs and, crucially, no Titanal in the skis. Other adjustments are steel edge thickness, thinner top sheets and running bases. Overall, we created a stable, lightweight alternative for those looking for a one-ski-does-it-all solution.
The shape of the classic Enforcer and Santa Ana is an essential part of the winning formula. This makes them accessible to a whole range of skiers, being fun and fast on almost all terrain. We wanted to take that shape and make it more accessible for uphill, as well as down. With the Unlimited, what we lose in outright stability at high speed is more than made up for by being more than 40% lighter, yet leaving a fun and playful ski, so that when you earn your turns they’re worth it.
AM: Are there any new products that you’re excited about this winter and can you give us a sneak peak of what we might see in the future?
MR: We’re really excited to see how the market likes the new Double Core piste skis. This tech was first launched in the Belle series, but now we’ve used it in our most well-known Dobermann and Spitfire ranges too. Double Core skis take an already great design and make it even easier to handle by removing vibration right in the middle of the core, before it can get going.
AM: And finally, what is your favourite ski of all-time and what makes it so special?
MR: I’m pretty flexible in my choice of skis, being privileged to use what fits the conditions. If I have to pick one, it has to be the first Enforcer 100, which brought us into a total new era and how we are seen as a ski brand. But there are many more models I could pick, from my experience and adventures over the years…